Grasping Welding WPS Standards: Ideal Practices and Techniques for Quality Welds
In the world of welding, grasping Welding Procedure Requirements (WPS) requirements is an important part that straight influences the top quality and honesty of welds. Following these criteria makes certain uniformity and dependability in welding outcomes. Nevertheless, achieving excellence in welds exceeds merely recognizing the requirements; it includes applying best practices and techniques that elevate the craft to a level of accuracy and skill that distinguishes the standard from the extraordinary. As we browse via the complexities of welding WPS standards, discovering essential understandings and strategies for achieving top-tier welds will be paramount for welders looking for to stand out in their craft and produce welds that stand the test of time.
Understanding Welding WPS Standards

Inspectors count on WPS documentation to confirm that welding procedures are being followed properly and that the resulting welds are of high top quality. Engineers utilize WPS requirements to design welding procedures that guarantee the longevity and integrity of bonded frameworks.
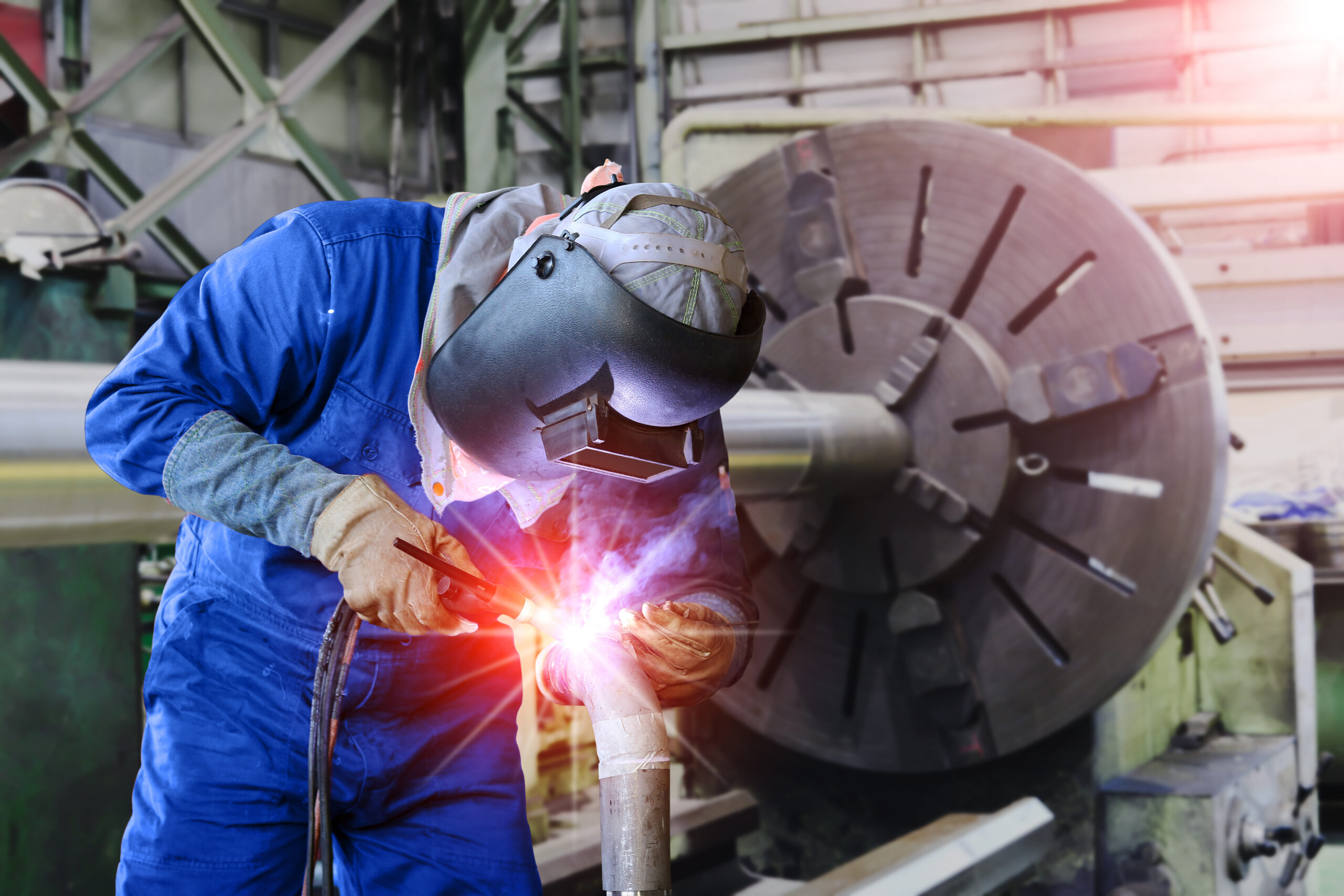

Crucial Tools for Top Quality Welds
Mastering welding WPS standards is vital for welders to effectively utilize the crucial devices required for generating top quality welds. The type of welding machine needed depends on the welding procedure being made use of, such as MIG, TIG, or stick welding. Cable brushes and chipping hammers are essential for cleansing the weld joint prior to and after welding to eliminate any kind of pollutants that can impact the high quality of the weld.
Key Strategies for Welding Success
To achieve welding success, one must grasp the vital strategies crucial for producing high-quality welds. One essential strategy is keeping the proper arc size. Keeping the electrode at the optimum range from the work surface is important for creating strong, consistent welds. Additionally, regulating the traveling rate is vital. Relocating as well promptly can result in insufficient infiltration, while relocating also gradually can lead to too much warm input and prospective navigate to this site defects. Proper control of the electrode angle is one more vital method. The angle at which the electrode is held can affect the grain shape and penetration of the weld. Additionally, making certain constant weapon angle and direction of traveling is essential for uniformity in the weld grain. Finally, preserving a stable welding and a steady hand setting throughout the process is essential to accomplishing precision and uniformity in the welds. By mastering these vital strategies, welders can elevate the quality of their job and attain welding success.
Ensuring Conformity With WPS Criteria
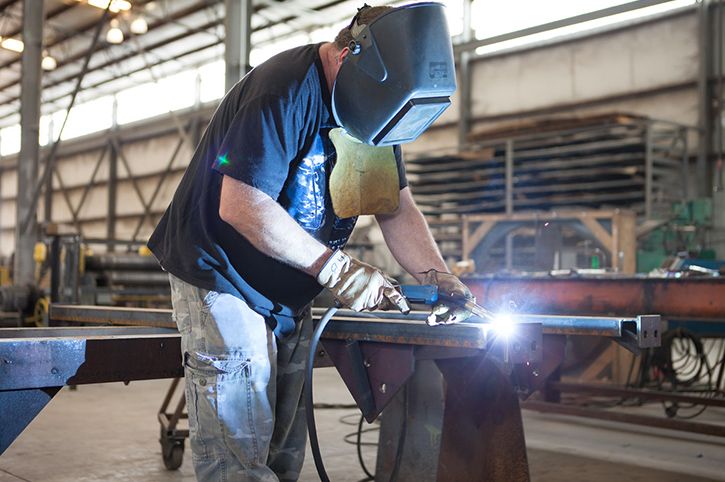
Additionally, keeping in-depth documents of welding criteria, tools calibration, and inspection outcomes is essential for showing compliance with WPS criteria. By faithfully sticking to WPS criteria, welders can make certain that their work meets the required quality degrees and adds to the overall success of the welding task.
Troubleshooting Common Welding Issues
When confronted with common welding issues, recognizing the origin is important for reliable troubleshooting. One common trouble is the existence of porosity in welds, usually triggered by impurities such as dampness, oil, or rust. To resolve this, ensuring correct cleaning of the base steel before welding and utilizing the correct shielding gas can dramatically lower porosity. An additional problem frequently come across is absence of blend, where the weld falls short to effectively bond with the base product. This can originate from poor warmth input or incorrect welding strategy. Adjusting specifications such as voltage, wire feed speed, or travel rate can aid enhance fusion. In addition, distortion, fracturing, and spatter are common welding challenges that can be reduced with appropriate joint preparation, consistent warmth control, and selecting the suitable welding consumables. By completely recognizing these typical welding concerns and their root creates, welders can effectively repair troubles and attain top quality welds.
Conclusion
In verdict, understanding welding WPS standards requires a thorough understanding of the standards, utilizing important tools, and executing vital methods for successful welds. Making sure compliance with WPS requirements is important for creating quality welds and avoiding common welding problems. By following ideal techniques and techniques, welders can accomplish consistent and trustworthy lead to their welding projects.
In the realm of welding, mastering Welding Treatment Specification (WPS) requirements is a vital component that directly influences the high quality and stability of welds.When diving into the world of welding techniques, a crucial element to comprehend is the relevance and complexities of Welding Treatment Requirements (WPS) requirements. WPS standards provide a detailed guideline for welding operations, guaranteeing uniformity, quality, and safety in the welding procedure. The type of welding equipment needed depends on the welding process being used, such as MIG, TIG, or stick welding.Achieving welding success via the proficiency of vital strategies requires you can check here an extensive understanding and adherence to Welding Treatment Specification (WPS) requirements.